Rapport des travaux pratiques : TP n° 1 : Modélisation et Simulation numérique
Rapport des travaux pratiques : TP n° 1 : Modélisation et Simulation numérique de l’emboutissage TP n° 2 : Usinage des pièces en utilisant le logiciel Catia V5 TP n° 3 : Pliage et Soudage Réalisé par : o SIMOUR Oussama o ALKHATIB Mohamed Khaled o LABIAD Anas Encadré par: Mr. BENMESSAOUD Génie Electromécanique 2020/2021 1 Modélisation et Simulation numérique de l’emboutissage I. Introduction : 1) Le principe de l’emboutissage : L’emboutissage profond consiste à fabriquer par formage généralement à froid une pièce creuse profonde (embout) à partir d’une feuille ou d’une plaque préalablement découpée (flan), et ce par action d’un poinçon et d’une matrice, et d’un serre-flan, sans réduction sensible de l’épaisseur. Le procédé est capable de fabriquer des pièces de formes circulaires (telles que des casseroles de cuisson), de formes carrées ou rectangulaires ainsi que d’autres formes complexes. Le principe de l’emboutissage profond est illustré à la figure ci-dessous. 2) Caractéristiques du logiciel utilisé : Le logiciel ABAQUS utilisé ici, a été développé depuis le début de la théorie des éléments finis et a été amélioré au fur et à mesure pour intégrer toutes les nouveautés de la théorie et des besoins de la recherche. ABAQUS est très largement utilisé dans les industries automobiles et aéronautiques. En raison du large spectre de ses capacités d'analyse et de sa bonne ergonomie, il est également très populaire dans les milieux universitaires, pour la recherche et l'éducation. ABAQUS fut d'abord conçu pour analyser les comportements non-linéaires. Il possède en conséquence une vaste gamme de modèles de matériau. Il est avant tout un logiciel de simulation par éléments finis de problèmes très variés en mécanique. Il est connu et répandu, en particulier pour ses traitements performants de problèmes non-linéaires. ABAQUS se distingue par sa capacité à traiter des problèmes multi-physiques de façon réaliste notamment en s’appuyant sur 4 points forts reconnus : Le traitement du contact, particulièrement facile de mise en données et robuste. 2 La modélisation de nombreux comportements matériels permettant de coller aux problématiques industrielles : Plastification et rupture des métaux. Hyper-élasticité des élastomères. Forte compressibilité des mousses. Porosité des matériaux géotechniques (sols, roches…). Compressibilité des fluides. Conductivité électrique... La capacité à traiter des problèmes de la statique à la dynamique rapide grâce à des méthodes adaptées et incluses dans la solution. Le couplage multi-physique via des procédures totalement intégrées et des ouvertures vers d’autres codes de calcul. II. Objectifs de la manipulation : Développer un modèle par éléments finis de simulation de l’emboutissage en utilisant le logiciel ABAQUS. Visualiser, étudier et analyser la distribution des contraintes sur le flan, l’outil, le serre flan et la matrice. Améliorer le modèle développé pour mieux prédire certaines grandeurs. I. Création du modèle : Pour commencer, on a créé un modèle sous le nom « Model 1 » en utilisant le menu « Model » de la barre d’outil. Partie 1 : Développement d’un modèle élément fini 3D 3 II. Définition des géométries : En utilisant le module « Parts » du modèle, on a créé les géométries suivantes : 1) Flan : On crée un cercle de centre (0,0) et de rayon 30 mm dans le plan XY, le flan est déformable de forme « solid » et la transformation utilisé est l’extrusion, l’esquisse du flan est le suivant : Après on effectue l’extrusion du flan avec une profondeur de 1 mm, le résultat final est le suivant : 4 2) Matrice : On dessine deux cercles concentriques de centre (0,0) et de rayon respectifs 8.5 mm et 30 mm dans le plan XY. L’esquisse obtenu est le suivant : Après on effectue l’extrusion de la matrice avec une hauteur de 60 mm, le résultat final est le suivant : 3) Serre-flan : En utilisant la même procédure de réalisation de la matrice, on réalise le serre-flan avec une forme similaire à la matrice mais avec une hauteur de 10 mm, le résultat final est le suivant : 5 4) Outil : On suit la même procédure de réalisation des pièces ci-dessous mais cette fois avec une transformation « Révolution ». L’outil est constitué de deux parties : Un cylindre de hauteur de 9 mm ; Une sphère de rayon de 5mm. L’esquisse obtenu est le suivant : Après on effectue une révolution de 360°, la pièce finale est la suivante : 6 III. Définition des matériaux des pièces : 1) Matériau du flan : Pour la définition des matériaux, on utilise la rubrique « Proprety », on clique sur l’icône « create material » , on choisit comme nom « Aluminium 3003 » et on entre les différentes propriétés suivantes : Pour l’affectation du matériau « Aluminium 3003 » au flan, on clique sur l’icône « section manager », on entre comme nom celui du matériau et on choisit comme type de matériau « Aluminium 3003 ». 7 On clique après sur l’icône « Section assignment manager » et on affecte le matériau « Aluminium 3003 » au flan : Le résultat final est le suivant : 2) Matériau de la matrice, serre-flan et l’outil : L’acier « AISI steel 4340 » est celui choisi pour la modélisation de la matrice, le serre-flan et l’outil. Pour le créer, on suit la même procédure du matériau « Aluminium 3003 ». Pour générer le comportement élasto-plastique de ce matériau, on utilise la loi de Jonson-Cook. On clique après sur l’icône « Section assignment manager » et on affecte le matériau « AISI steel 4340 » aux pièces, le résultat obtenu est le suivant : 8 I. Assemblage : Dans cette étape, on va créer une instance à partir des entités qu’on a créé dans le module « Part », on clique sur l’icône « Create Instance », On choisit les géométries et on commence à assembler en respectant plusieurs contraintes. L’instance créé est la suivante : Partie 2 : Assemblage et simulation de l’emboutissage 9 II. Définition des étapes de simulation : On utilise maintenant le menu « Step », on crée une étape sous le nom « Step » et on choisit comme type de de procédure « Static, general », après on clique sur « Basic » et on utilise la stabilisation automatique avec un facteur d’amortissement de 0.002. Après, on entre le nombre maximale d’incrémentation et les différentes tailles (initiale & minimale) : On sélectionne « Field Output Manager », on laisse le nom par défaut et on choisit « Step ». De même, on sélectionne « History Output Manager », on laisse le nom par défaut et on choisit « Step », on laisse les paramètres par défaut. 10 III. Gestion de contact : On va utiliser le module « Interaction » qui permet de spécifier toutes les interactions entre les différents parties et régions du modèle, qu’elles soient mécaniques, thermiques ou autres. Les différentes combinaisons qui existent sont : D’où : IV. Modélisation des sollicitations et des conditions au limite : Dans le module « Load », on clique sur l’icône « Load Manager », on donne comme nom « Pression-serre-flan » et comme type de force « Pressure », on choisit la surface supérieure du serre-flan, après on choisit comme distribution « total force » et une amplitude de 107 N. 11 On clique sur l’icône « Boundary Condition manager », on donne comme nom « Encastrement », comme catégorie « Mechanical », comme type « Encastre » et comme type d’étape « Initial ». Après, On choisit comme région d’application de la condition la surface inférieure de la matrice. On clique sur l’icône « Boundary Condition manager », on donne comme nom « Déplacement_outil », comme catégorie « Mechanical », comme type « Displacement » et comme type d’étape « Initial ». Après, On choisit comme région d’application de la condition la surface supérieure de l’outil. Dans la fenêtre « Boundary Condition manager », on sélectionne la condition « Déplacement_outil » à l’étape 1 et on clique sur Edit. Le résultat final est le suivant : 12 V. Maillage : Dans le module « Part », on choisit le flan puis on sélectionne le module « Mesh », on clique sur l’icône « Seed part », on entre 2 mm comme taille approximative de maillage et 0.1 mm dans la case de contrôle de la courbure, le résultat final est le suivant : Pour le maillage de l’outil, on entre une valeur de 1 mm comme taille approximative de maillage. Pour le serre-flan et la matrice, on entre 8 mm. D’où : VI. Lancement des calculs : Dans le module « Job », on sélectionne l’icône « Job manager » et on crée une simulation sous le nom « Simulation-1 ». 13 On utilise le module « visualization » uploads/s3/ cr-global-des-travaux-pratiques.pdf
Documents similaires
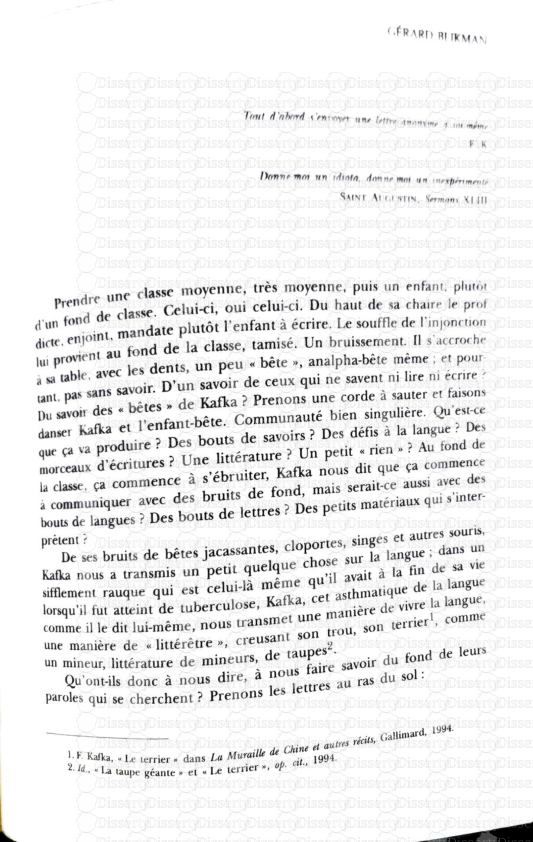
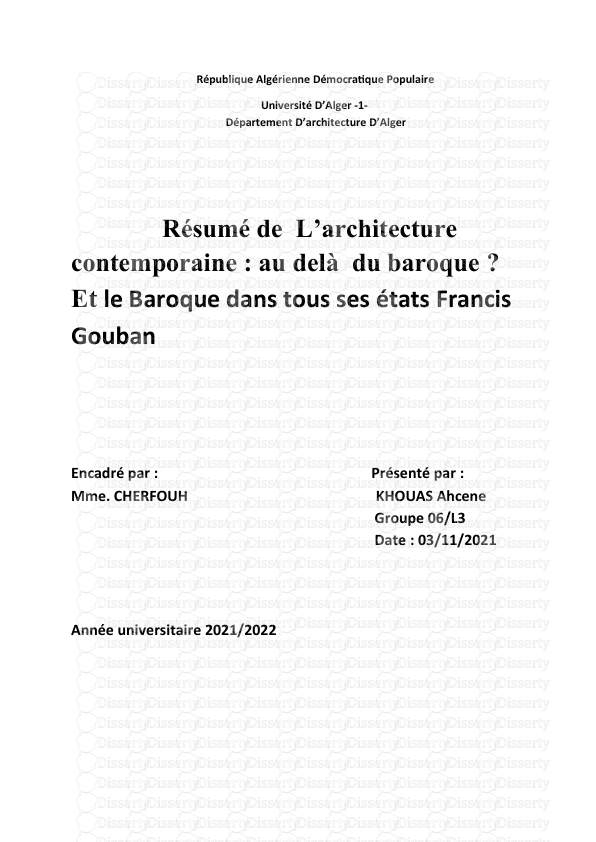
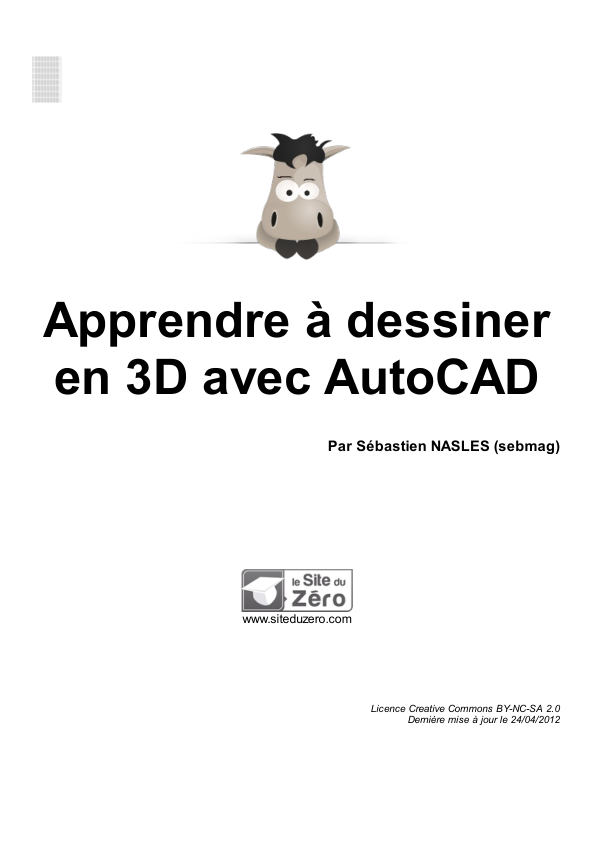
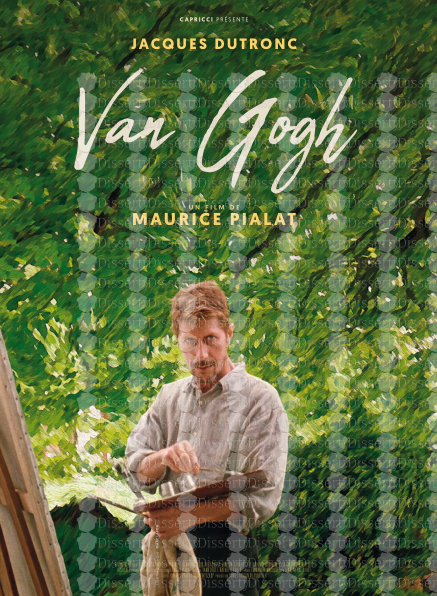
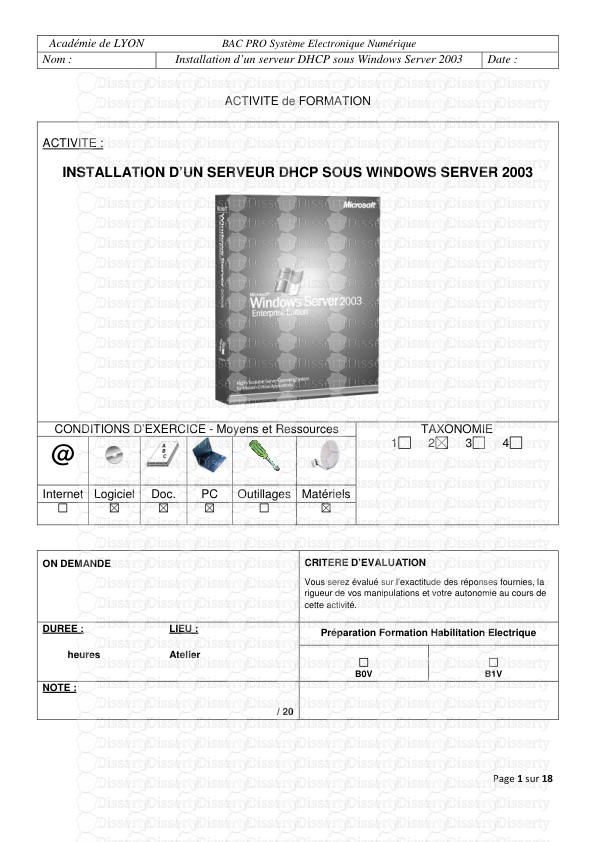
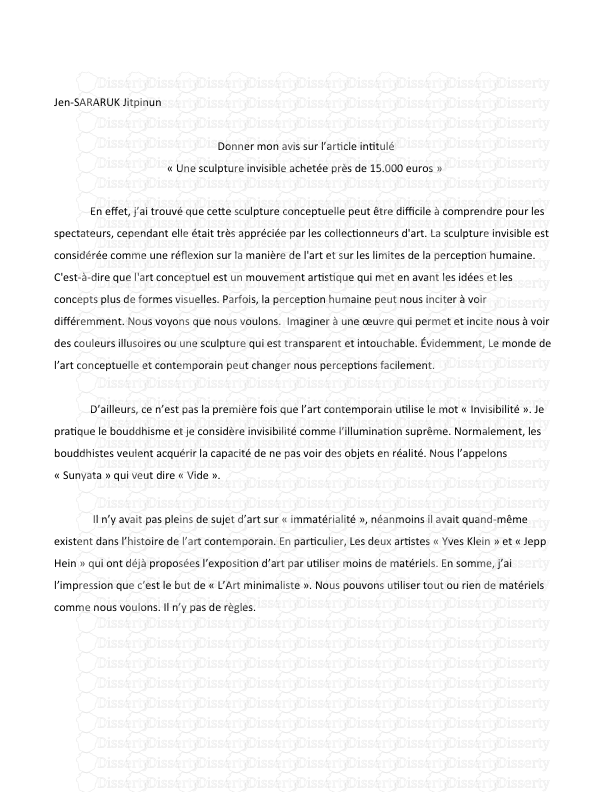
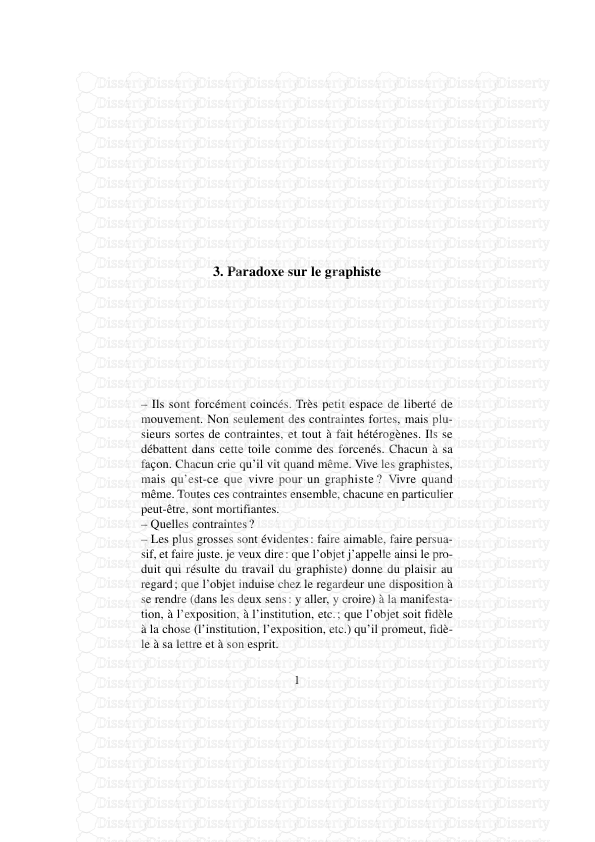
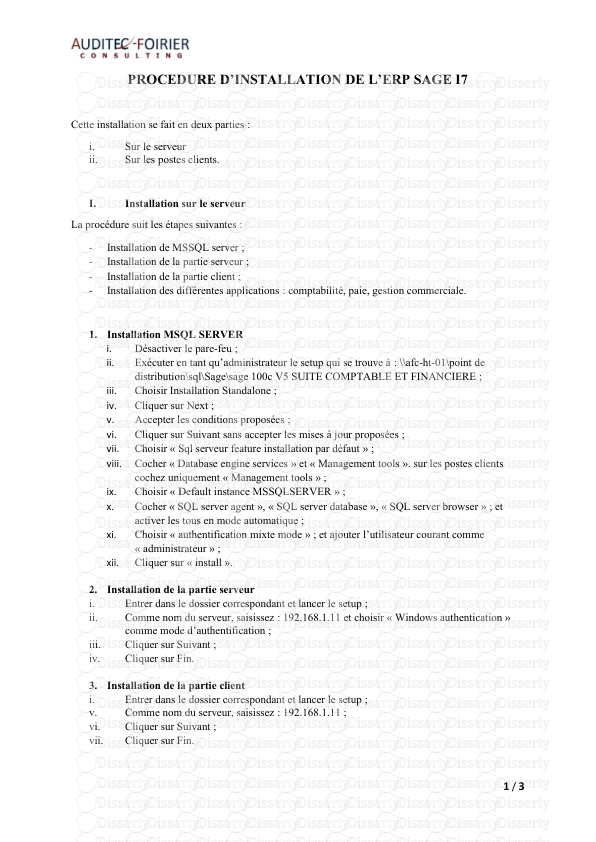
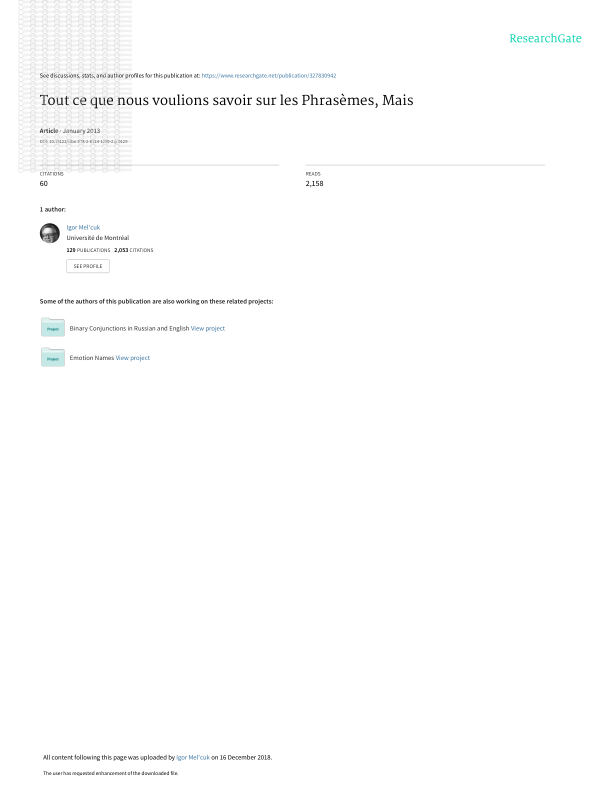
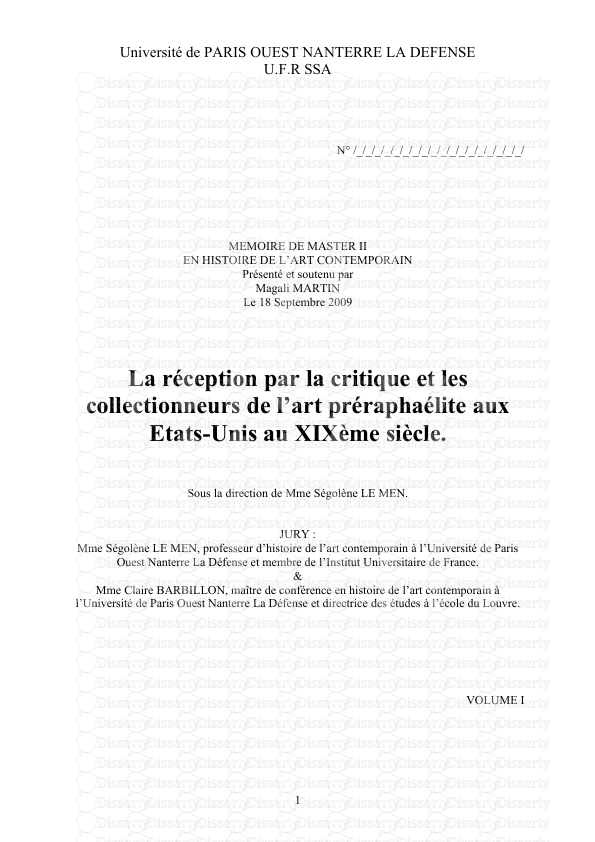
-
34
-
0
-
0
Licence et utilisation
Gratuit pour un usage personnel Attribution requise- Détails
- Publié le Apv 27, 2022
- Catégorie Creative Arts / Ar...
- Langue French
- Taille du fichier 3.0658MB