Toute reproduction sans autorisation du Centre français d’exploitation du droit
Toute reproduction sans autorisation du Centre français d’exploitation du droit de copie est strictement interdite. © Techniques de l’Ingénieur, traité Sécurité et gestion des risques SE 4 060 − 1 MOSAR Présentation de la méthode par Pierre PERILHON Ingénieur de l’École nationale supérieure des arts et métiers (ENSAM) Ancien responsable de sécurité-sûreté au Commissariat à l’énergie atomique (CEA) ’analyse des risques d’une installation industrielle est une démarche complexe car cette dernière est elle-même une structure complexe constituée de machines, de stockages, en interaction entre eux, avec les opérateurs ainsi qu’avec l’environnement. Pour se donner le maximum de chances de mettre en évidence la majorité des risques d’une installation, une méthode logique est proposée : la méthode organisée systémique d’analyse des risques ou MOSAR. Elle fait appel à la modélisation systémique [1] car après avoir décomposé l’instal- lation en sous-systèmes et recherché systématiquement les dangers présentés par chacun d’entre eux, ces sous-systèmes sont remis en relation pour faire appa- raître des scénarios de risques majeurs. Cette partie de l’analyse est une APR (Analyse préliminaire des risques) évoluée car elle ne se contente pas de passer l’installation au crible de grilles préétablies issues du retour d’expérience. Elle construit, à partir d’une modélisation des différents types de dangers par le modèle MADS (Méthodologie d’analyse de dysfonctionnement des systèmes), les scénarios possibles. La négociation d’objectifs permet de hiérarchiser ces scéna- rios. La recherche systématique de barrières permet de neutraliser ces scénarios 1. Nécessité d’une méthode d’analyse des risques d’une installation industrielle .............................................................. SE 4 060 - 2 1.1 Problématique.............................................................................................. — 2 1.2 Les besoins d’analyse de risques............................................................... — 3 1.3 Les outils existants ...................................................................................... — 3 1.4 Nécessité d’une méthode ........................................................................... — 3 2. Structure générale de la méthode MOSAR ...................................... — 4 2.1 Les deux modules et les dix étapes ........................................................... — 4 3. Modèles mis en œuvre : MADS............................................................ — 4 3.1 Description de MADS.................................................................................. — 4 3.2 Applications à une démarche méthodique ............................................... — 5 4. Différents modes de mise en œuvre de la méthode ...................... — 7 4.1 MOSAR comme boîte à outils .................................................................... — 7 4.2 Les parcours de MOSAR............................................................................. — 8 4.3 Genèse de scénarios dans l’analyse de risques d’un site industriel....... — 9 4.4 Extraits d’exemple d’analyse en conception d’une installation .............. — 10 4.5 Extrait d’exemple d’analyse en diagnostic d’une installation existante. — 13 5. Avantages de la méthode ...................................................................... — 14 5.1 La réponse aux besoins .............................................................................. — 14 5.2 Exhaustivité.................................................................................................. — 15 5.3 Coordination des outils............................................................................... — 15 5.4 Souplesse..................................................................................................... — 15 5.5 Mise en œuvre en situation opérationnelle et pédagogique................... — 15 Références bibliographiques ......................................................................... — 16 Pour en savoir plus........................................................................................... Doc. SE 4 062 L MOSAR ______________________________________________________________________________________________________________________________ Toute reproduction sans autorisation du Centre français d’exploitation du droit de copie est strictement interdite. SE 4 060 − 2 © Techniques de l’Ingénieur, traité Sécurité et gestion des risques et leur qualification dans le temps en assure la pérennité. La démarche peut se poursuivre par une analyse détaillée de type sûreté de fonctionnement avec mise en œuvre d’outils comme les AMDEC (Analyse des modes de défaillance, de leurs effets et de leur criticité) (cf. article AMDEC-Moyen [AG 4 220] dans le traité l’Entreprise industrielle), les arbres de défaillances (cf. article Arbres de défaillance, des causes et d’événement [SE 4 050] dans ce traité), HAZOP (Hazard and Operability study) [4]. Sa constitution modulaire permet une grande souplesse d’utilisation. Elle se termine sur la construction des plans d’intervention. Le modèle MADS, élaboré dans les années 1980 par un groupe d’ingénieurs du CEA (Commissariat à l’énergie atomique) et d’universitaires de l’IUT de sécurité de Bordeaux, est une modélisation systémique générale du danger mise en œuvre ici de manière spécifique dans la méthode MOSAR. La méthode MOSAR complète fait l’objet d’un support [5], d’un résumé [8] et d’un logiciel d’apprentissage [6]. Cet article constitue la première partie d’une série consacrée à la méthode MOSAR : — MOSAR - Présentation de la méthode [SE 4 060] ; — MOSAR - Cas industriel [SE 4 061]. Terminologie Problématique Une certaine façon de poser un ou des problèmes propres à une notion ou à un domaine de connaissance. Méthodologie Réflexion qui a pour objet d’examiner la nature, la valeur et le choix des matériaux avec lesquels nous pouvons construire notre connaissance en vue de déterminer à quels usages ils sont propres ou impropres. Méthode Programme réglant d’avance une suite d’opérations à accomplir et signalant certains errements à éviter, en vue d’atteindre un résultat déterminé. Outils Procédés techniques de calcul ou d’expérimentation utilisés pour le développement d’une méthode. Analyse de risques Toute démarche structurée permettant d’identifier, évaluer, maîtriser, manager et gérer des risques et notamment les risques industriels. 1. Nécessité d’une méthode d’analyse des risques d’une installation industrielle 1.1 Problématique Une installation industrielle peut être modélisée comme un sys- tème ouvert sur son environnement, et composé essentiellement de matériels (M1, M2, M3...) et d’opérateurs (O1, O2, O3...), en inter- action entre eux et avec l’environnement (figure 1). Les matériels (machines, stockages, appareils, bâtiments...) peuvent : — interagir de manière séquentielle (séquences linéaires, paral- lèles ou en réseaux) lorsqu’ils constituent des chaînes de fabrica- tion ; — ou être isolés. Les opérateurs sont tous les acteurs de l’installation depuis le responsable jusqu’à l’exécutant. Ils peuvent être aussi isolés ou en relation à travers des hiérarchies linéaires ou parallèles, des groupes en réseau ou des structures diverses. Analyser les risques d’une installation va consister essentiel- lement à identifier les dysfonctionnements de nature technique et opératoire (opérationnelle, relationnelle, organisationnelle) dont l’enchaînement peut conduire à des événements non souhaités par rapport à des cibles (individus, populations, écosystèmes, systèmes matériels ou symboliques). Figure 1 – Modélisation d’une installation industrielle O1 O2 O3 O4 M2 M1 M3 ______________________________________________________________________________________________________________________________ MOSAR Toute reproduction sans autorisation du Centre français d’exploitation du droit de copie est strictement interdite. © Techniques de l’Ingénieur, traité Sécurité et gestion des risques SE 4 060 − 3 Ces dysfonctionnements proviennent des matériels, de leurs liaisons et de leur proximité, ainsi que des opérateurs, de leurs liaisons entre eux et avec les matériels. Il est possible d’imaginer analyser les risques d’une installation à un instant donné, par exemple à t1 ou à t2 . On dira alors que l’on a travaillé dans une coupe synchronique de l’installation. Mais entre les instants t1 et t2, l’installation a évolué (diachronie). Il est donc impossible de faire l’analyse des risques d’une installation dans sa diachronie. Tout au plus pourra-t-on la pratiquer à certains moments discrets de cette dernière, que nous allons identifier, et l’on pourra éventuellement mettre en évidence des risques de transition entre ces moments. Ces moments de vie d’une installation ou phases de vie sont les suivants : — conception (CO). C’est le travail de bureau d’études qui définit un cahier des charges, un dossier d’appel d’offre, un descriptif, un dossier de réalisation. Il est évidemment très intéressant d’analyser les risques en conception car on peut intégrer leur maîtrise dès le départ et cela est moins coûteux que de modifier par la suite l’instal- lation pour des raisons de sécurité ; — montage (MO). C’est la phase de réalisation qui correspond au chantier avec des risques très spécifiques notamment de manu- tention ; — essais (ES) ou recette. C’est la phase qui permet de faire les vérifications de conformité par rapport au cahier des charges. Elle est souvent l’objet de risques spécifiques car les éléments de l’ins- tallation peuvent être testés jusqu’à leurs performances maximales voire au-delà ; — exploitation. Cette phase correspond aux périodes de mise en œuvre de l’installation. On peut la diviser en : • fonctionnement normal (on la symbolisera par EX) : l’installa- tion fonctionne dans le cadre de ses caractéristiques nomina- les. Elle peut alors générer des nuisances et être la source d’accidents, • maintenance qui comprend : l’entretien (EN), préventif ou curatif, le dépannage (DE), • arrêt (AR). L’installation peut présenter des dangers spéci- fiques à l’arrêt ; — transformation. Cette phase concerne les transformations générant des risques spécifiques liés aux chantiers nécessaires pour les réaliser ou à l’installation transformée ; — démantèlement (DEM) ou déconstruction. Cette phase cor- respond aussi à une phase de chantier très spécifique. Il est donc nécessaire de préciser la phase de vie de l’installation dans laquelle l’analyse est réalisée. Il est aussi possible de se situer dans une phase et de faire apparaître les risques principaux des autres phases. 1.2 Les besoins d’analyse de risques Nota : le lecteur consultera utilement sur ce sujet l’article Importance de la sécurité dans l’entreprise [AG 4 600] dans le traité l’Entreprise industrielle. Les besoins dans ce domaine sont multiples. Si la connaissance et la maîtrise des risques de l’entreprise sont tout d’abord un problème d’éthique, ce sont aussi un moyen : — d’accroître la confiance du public, du personnel, des investis- seurs et de conserver une bonne image de marque ; — de satisfaire les contraintes réglementaires multiples : Code du travail, installations classées pour la protection de l’environnement, circulaire Seveso, règles des services de prévention des CRAM (Caisses uploads/Management/ techniques-de-l-x27-ingenieur-se-4-060-mosar-presentation-de-la-methode.pdf
Documents similaires






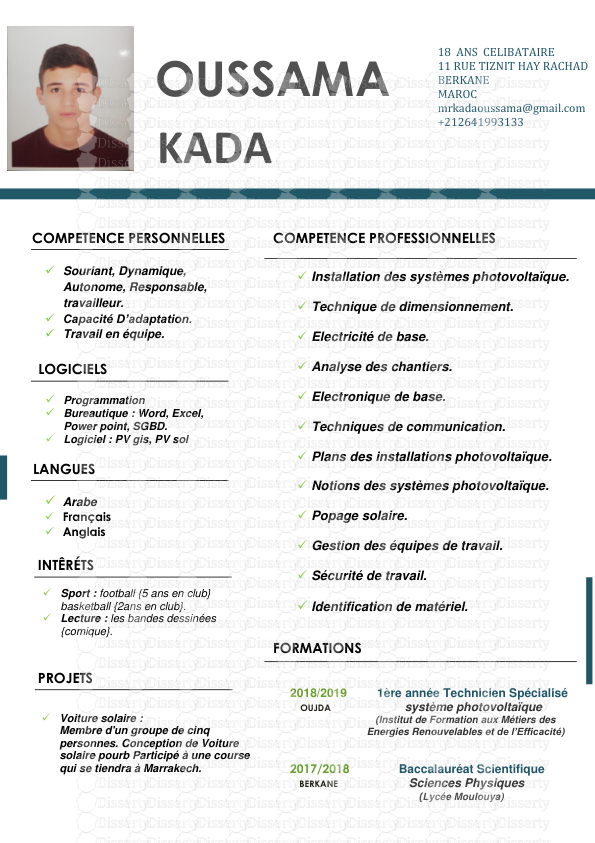



-
64
-
0
-
0
Licence et utilisation
Gratuit pour un usage personnel Attribution requise- Détails
- Publié le Mar 31, 2021
- Catégorie Management
- Langue French
- Taille du fichier 0.3217MB