Sur l'application de la méthode ABC/ABM au calcul des coûts de la maintenance H
Sur l'application de la méthode ABC/ABM au calcul des coûts de la maintenance Houda El Aoufir, Driss Bouami, Mohammed Hicham Mouzdahir Dans Revue française de gestion 2004/5 (no 152), pages 35 à 44 Article Dans un environnement de plus en plus concurrentiel, la maîtrise des coûts devient primordiale. La maintenance des équipements joue un rôle de plus en plus grand dans la réalisation des objec tifs requis par la production à un coût minimal. De la pertinence des décisions prises au niveau politique (internaliser ou externaliser la maintenance), au niveau stratégique ou au niveau opérationnel, dépend l’efficience d’un service de maintenance. La mise en place d’un système de gestion des coûts de la maintenance devient alors un atout important pour les industriels, les prises de décision étant largement tributaires de la qualité des indicateurs économiques. Dans cet article, nous proposons l’utilisation de la méthode ABC/ABM en gestion de la maintenance comme outil de calcul des coûts et de pilotage des activités de la maintenance. Après un bref exposé des avantages potentiels de cette méthode par rapport aux méthodes de contrôle de gestion traditionnelles, nous proposons une démarche en vue de son application au contexte choisi, enfin nous présentons les résultats d’une expérimentation dans une industrie agro-alimentaire et nous dégageons des conclusions relatives à l’applicabilité de la méthode dans le contexte industriel marocain. I. – L’IDÉE D’APPLIQUER ABC/ABM EN GESTION DE LA MAINTENANCE 1. Le contexte industriel et la problématique de la gestion des coûts de maintenance De multiples développements ont été réalisés ces quatre dernières décennies en matière de maintenance. Ces développements (Monchy, 2003; El Aoufir et Bouami, 2003; Frederic, 2003; Heng, 2002) ont couvert les aspects techniques (maintenance prédictive, techniques de contrôle non destructif, systèmes experts, GMAO : gestion de maintenance assistée par ordinateur), les méthodes, concepts et outils de maintenance rationnelle (Life Cycle Cost, RCM : Reliability Centred Maintenance/MBF : maintenance basée sur la fiabilité, TPM : Total Productive Maintenance) et la recherche en sûreté de fonctionnement et en optimisation de la maintenance. Ils ont permis, dans le nouveau contexte de l’économie mondiale, une progressive migration de la fonction maintenance de l’état de fonction « budgétivore » à l’état de fonction productive (de disponibilité, de sécurité, etc.) et donc « source de profit ». Cependant, malgré cette prise de conscience, et du fait de la nature des tâches traditionnellement très techniques dans les services de maintenance, les moyens de mesure et d’analyse des indicateurs économiques sont encore très mal adaptés à des objectifs de suivi des activités, de rationalisation des pratiques et d’amélioration continue. Nos interventions auprès d’industriels, dans le cadre d’activités de formation, d’encadrement de projets et de conseil en gestion de la maintenance, nous ont permis de constater que bien souvent le suivi des coûts [2] de maintenance se limitait à une simple imputation par centre de charge ou par rubrique de frais. Or ce type d’imputation permet uniquement de constater de façon plus ou moins réaliste des faits passés, il ne permet pas d’en comprendre les causes ni de réagir. Nous avons également constaté que les charges indirectes telles que les dépenses liées à la préparation des interventions, n’étaient pas prises en compte. Les systèmes de gestion permettent donc un suivi plus ou moins détaillé des consommations passées mais sont tout à fait incapables de lier les coûts aux performances et de fournir une aide à l’analyse des dysfonctionnements et à la prise de décision. Outre le besoin en moyens de calcul de coûts, nous avons ressenti un réel besoin en formalisation des pratiques, en capitalisation du savoir-faire, en apprentissage organisationnel et en méthodes de pilotage. 2. Apport de la méthode ABC/ABM dans le contexte de l’étude Nos lectures sur la méthode ABC/ABM (Ravignon et al., 2000; Lorino, 1998; Lorino et Tarondeau, 1998; Mevellec, 1991). nous ont permis de voir immédiatement son intérêt potentiel dans la résolution des problèmes posés. En effet, la méthode ABC/ABM peut : fournir le moyen de modéliser une chaîne de valeur (ici la création de fiabilité, de maintenabilité, de disponibilité ou de sécurité des installations) par un ensemble de processus (par exemple, la maintenance curative) constitués d’activités (diagnostiquer, préparer les ressources, intervenir, renseigner un rapport, etc.) et consommant des ressources (main-d’œuvre, pièces, outillages, méthodes, etc.) ; favoriser la responsabilisation des acteurs par le travail en équipe (les processus étant généralement transversaux), la formalisation des pratiques (nécessité de décrire la manière de réaliser les activités), la compréhension des mécanismes (relations causes à effets) et la capitalisation du savoir-faire; permettre d’évaluer, de façon plus fiable, les coûts des activités de maintenance mais également d’autres indicateurs de performance (délais des interventions, disponibilité, etc.) afin de mesurer la pertinence des choix opérationnels, stratégiques, politiques et de les améliorer. Ce dernier point contribuerait à abattre les cloisons entre la culture opérationnelle de l’atelier de maintenance et la culture économique des décideurs. II. – DÉMARCHE PROPOSÉE 1. Vers un système de mesure plus fiable des coûts de maintenance Les principales étapes identifiées sont les suivantes : Étape 1. Définir les objectifs stratégiques de la maintenance. Ces objectifs peuvent être l’amélioration de la fiabilité, de la maintenabilité, de la disponibilité [3], la réduction des risques d’incidents nuisibles à la qualité de la production ou au respect de l’environnement, etc. Cette première étape permettrait de détecter des anomalies telles que l’utilisation des moyens de la maintenance à des fins non liées aux objectifs. Exemple : utiliser les ressources de la maintenance pour l’entretien du jardin. Étape 2. Définir les processus [4] de maintenance. Cette étape a pour objectif de définir les différents moyens utilisés pour répondre aux objectifs stratégiques. Exemple : le processus de maintenance corrective permet de remettre en état un équipement défaillant. Le processus de maintenance préventive permet de réduire les probabilités de défaillance. Étape 3. Définir les activités constituant chaque processus de maintenance. Une activité est un ensemble de tâches élémentaires faisant appel à un savoir-faire spécifique permettant d’aboutir à une réalisation matérielle ou immatérielle à partir d’un ensemble de ressources. Exemples : préparer un plan de maintenance, réparer une panne, rédiger un rapport, mettre à jour un dossier machine. Le degré (ou volume) de sollicitation d’une activité doit être mesurable à l’aide d’une unité de mesure appelée inducteur d’activité (voir exemple dans le tableau 1). Étape 4. Identifier les ressources mises en œuvre dans les activités et les quantifier. Les ressources de la maintenance peuvent être classées selon la logique des 5 M (main-d’œuvre, matières et consommables, matériel et outillages, méthodes et milieu). À chaque ressource doit être associée une unité d’œuvre permettant d’en mesurer la consommation (nombre d’heures de travail, nombre d’unités consommées, etc.) Étape 5. Valoriser les coûts des activités et des processus de maintenance pour différents objets de coût. Les objets de coût sont fonction du découpage géographique, matériel ou fonctionnel de l’outil de production (exemple : usine/atelier/équipement). Cette étape permettrait de retrouver les indicateurs fournis par les systèmes de gestion traditionnels mais avec une imputation plus fine et plus fiable des coûts. Étape 6. Déployer les objectifs stratégiques sur les processus et valoriser transversalement les processus de maintenance Nous entendons par déploiement des objectifs sur les processus, la détermination de la contribution de chaque processus dans la réalisation des objectifs stratégiques. La valorisation de ces processus permettrait de confronter les coûts des ressources mises en œuvre à la contribution aux objectifs et, par voie de conséquence, réaliser une première transition vers un système de diagnostic et de pilotage. Nous récapitulons dans la figure 1 la logique de la démarche proposée. 2. Passer d’un système de mesure des coûts vers un système de pilotage de la maintenance Afin de passer d’une logique de mesure des coûts à une logique d’évaluation de l’efficience [5], de diagnostic des dysfonctionnements et de pilotage des activités, nous proposons les étapes suivantes (schématisées dans la figure 2): Étape 7. Associer aux objectifs stratégiques de maintenance des indicateurs de pilotage. À titre d’exemple, si on veut suivre et améliorer la disponibilité, on associera à cet objectif la mesure de la disponibilité (temps de bon fonctionnement rapporté au temps de requis de fonctionnement). La sécurité sera suivie en définissant une échelle de criticité et en mesurant le nombre d’incidents critiques. La qualité sera évaluée par un taux de production conforme. On notera d’ores et déjà que cette approche sera d’autant plus simple à mettre en œuvre dans des entreprises rompues à la logique « total productive maintenance ou maintenance » basée sur la fiabilité. Figure 1 SCHÉMATISATION DES ÉTAPES 1 À 6 DE LA DÉMARCHE Figure 1 Figure 2 SCHÉMATISATION DES ÉTAPES 7 À 9 DE LA DÉMARCHE Figure 2 Figure 3 CONFIGURATION D’UNE LIGNE DE PRODUCTION PRODUITFINI Figure 3 Étape 8. Identifier les moyens d’action sur les objectifs stratégiques. Après confrontation des objectifs visés (par exemple améliorer la disponibilité de 30 % sur un horizon prévisionnel donné) avec les résultats obtenus (variation effective de la disponibilité), il sera nécessaire d’analyser le système productif (hommes, machines, matières, méthodes) en vue d’identifier les causes premières des dysfonctionnements. Une grande uploads/Management/ abc 1 .pdf
Documents similaires








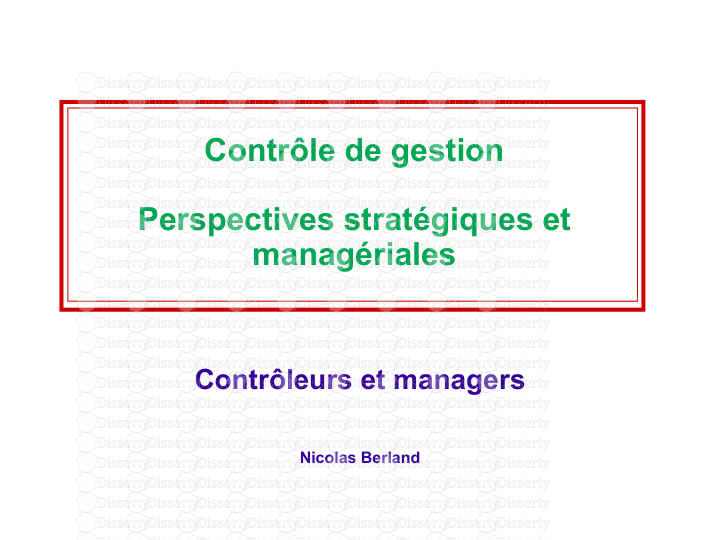

-
38
-
0
-
0
Licence et utilisation
Gratuit pour un usage personnel Attribution requise- Détails
- Publié le Mai 13, 2022
- Catégorie Management
- Langue French
- Taille du fichier 0.0457MB