COURS MISE EN ŒUVRE D’UNE MAQUETTE ELECTRONIQUE page 1/4 MISE EN ŒUVRE D’UNE MA
COURS MISE EN ŒUVRE D’UNE MAQUETTE ELECTRONIQUE page 1/4 MISE EN ŒUVRE D’UNE MAQUETTE ÉLECTRONIQUE I. Objectifs Savoir réaliser une maquette électronique à partir d’un schéma structurel et d’un cahier des charges. - Valider le fonctionnement de la maquette : conformité avec l’analyse fonctionnelle et structurelle. - Réaliser un dossier ou manuel technique. II. Présentation Une maquette électronique est constituée d’un circuit imprimé sur lequel sont soudés des composants (composants discrets, circuits intégrés, capteurs, actionneurs, etc.) réalisant une ou plusieurs fonctions. III. Circuit imprimé Un circuit imprimé est constitué d’un support isolant (époxy ou Bakélite) percée de trous dans lesquels sont enfilées les broches de raccordement des composants du montage à câbler. Le dos de ce circuit imprimé porte des pistes cuivrées matérialisant les connexions électriques devant relier les composants entre eux. Les broches des composants sont soudées directement sur ces pistes qui peuvent recouvrir les deux faces de la plaquette (technique double face ou multicouche). On réalise les circuits imprimés à l’aide d’un typon et d’une plaque pré sensibilisée. IV. Réalisation du typon. Un typon est un masque transparent (papier calque, film plastique) représentant l’implantation structurelle d’un circuit électrique tenant compte des dimensions réelles des composants (contrairement au schéma structurel). Sur ce masque, chaque trait opaque représente une piste de cuivre (pour les plaques pré sensibilisées positives). Il peut être réalisé à la main, au feutre de dessinateur industriel ou grâce à des pistes carbones sous forme de transfert, soit à l’aide d’un outil de C.A.O. (logiciel de placement routage). La réalisation du typon doit tenir compte des contraintes énoncées dans le cahier des charges (taille du circuit imprimé, encombrement des composants, etc.). V. Gravure d’une plaque pré sensibilisée Une plaque pré sensibilisée est constituée d’une feuille isolante et d’une feuille de cuivre contrecollées recouverte d’une résine photosensible positive. Cette résine, normalement insoluble dans un solvant appelé révélateur, possède la propriété d’y devenir soluble après exposition à un rayonnement ultra violet. Ce changement de propriété est dû à la destruction par le rayonnement de la structure chimique du produit : on parle de dépolymérisation. Si une couche sensible réalisée au moyen d’une résine positive est exposée au UV à travers un document comportant des zones opaques et des zones transparentes (ex : un typon imprimé sur calque), les parties de la couche correspondant aux zones transparentes vont se trouver insolées, donc disparaître lors de l’immersion dans le révélateur. En revanche, seules les zones correspondant aux parties opaques du document (pistes) vont rester intactes. Une fois insolée et révélée, la plaque est trempée dans un agent d’attaque chimique (perchlorure de fer) qui va éliminer le cuivre qui n’est pas protégé par la résine : il ne reste sur la plaque que les pistes du circuit électrique. La gravure terminée, un dissolvant approprié permettra de débarrasser la pièce de la résine ayant terminé son office. Vue en coupe d'une plaque pré sensibilisée Couche de résine positive Cuivre Isolant (époxy ou Bakélite) 1- Exposition Ultra violets Typon Résine exposée Résine vierge 2- Développement 3- Attaque chimique 4- Nettoyage au dissolvant Piste de cuivre Fig. V-a. Déroulement des opérations de photogravure d'une plaque de circuit imprimé (résine positive). Dessin d'une piste COURS MISE EN ŒUVRE D’UNE MAQUETTE ELECTRONIQUE page 2/4 VI. Etamage ou argenture des circuits imprimés Cette étape facultative permet d’éviter l’oxydation du cuivre et facilite le soudage des composants. Elle peut être réalisée par trempage du circuit imprimé dans un bain d’étain en fusion ou dans une solution saline du métal à déposer (étamage à froid). VII. Le perçage Le diamètre de perçage dépend de la taille des broches des composants. Il est compris entre 0,8 et 1,5 mm pour les composants électroniques courants. La vitesse de perçage pour ces petits diamètres doit être de l’ordre de 10 à 15 000 tr/min. Plus le diamètre est gros plus la vitesse doit être réduite. Les outils de CAO de placement routage permettent de générer automatiquement les plans de perçage des circuits imprimés. Ils peuvent également générer des fichiers permettant de piloter des perceuses ou poinçonneuse à commande numérique afin d’automatiser la production de circuits imprimés. Chaque trou peut être métallisé afin d’assurer les éventuelles liaisons électriques entre les couches du circuit imprimé (via). VIII. Le soudage Il existe plusieurs types de soudage : - Le soudage par vague utilisé dans l’industrie permet de souder l’ensemble des composants en une seule fois. Il faut donc placer auparavant tous les composants sur le circuit imprimé soit manuellement soit automatiquement en utilisant une machine d’aide au positionnement (surtout utilisée pour les CMS : Composants Montés en Surface). Les outils de CAO de placement routage permettent de générer les fichiers pilotant ces machines. - L’autre type de soudage, le soudage manuel, est réservé pour la fabrication de prototypes ou de pré série. Comme les composants doivent être plaqués contre le circuit imprimé, il est préférable de souder ceux qui ont un faible encombrement en premier (ex : diodes, résistances). Ils sont ainsi maintenus entre le plan de travail et le circuit imprimé. Les autres composants seront soudés par ordre croissant de leur volume. La jonction entre le composant et le circuit imprimé est réalisée à l’aide d’un fer à souder et de soudure (60% d’étain avec décapant incorporé). Il est important de ne pas trop chauffer les composants (risque de détérioration) ni les pistes imprimées qui risque de se décoller. De plus, si la soudure est surchauffée, tout le décapant s’évapore, la soudure devient terne et n’assure plus efficacement la liaison électrique entre le circuit imprimé et le composant : on parle de soudure sèche qui provoque des pannes difficilement décelables. On obtient également des soudure sèches si la broche du composant ou la pastille n’est pas suffisamment chauffée (voir fig. VIII-c). Pour obtenir de belles soudures, il faut maintenir la panne du fer à souder dans un constant état de propreté (en la débarrassant des résidus de soudure à l’aide d’une éponge humide). Remarque : certains composants sont très sensibles aux chocs électrostatiques (technologie FET, etc.) et peuvent être détruit lors de leur câblage. Il est donc nécessaire de mettre à la terre le fer à souder, le plan de travail ainsi que l’opérateur (bracelet conducteur relié à la terre par une résistance de 1MΩ). Fig. VIII-c. Exemples de soudures Soudure solidaire à la broche du composant uniquement Broche de composant Pastille Soudure solidaire à la pastille uniquement Soudure solidaire à la pastille et à la broche du composant Soudure incorrecte Soudure incorrecte Soudure correcte Fig. VIII-b. Soudure manuelle d'un composant à piquer. Piste (pastille) Soudure Fer à souder Panne du fer à souder Soudure en bobine (étain + décapant) Fig. VIII-a. Soudure par vague d'un composant à piquer. Etain en fusion Piste (pastille) Soudure Sens de la vague COURS MISE EN ŒUVRE D’UNE MAQUETTE ELECTRONIQUE page 3/4 IX. Le vernissage Le vernissage des circuits imprimés protège les connexions contre l’humidité et l’oxydation : on parle de vernis épargne (couleur verte ou rouge). Le coté composant peut être également verni ce qui améliore la rigidité du câblage en collant les composants sur la plaquette. On utilise en général un vernis incolore. Remarque : les outils de CAO de placement routage génèrent des fichiers permettant de créer un film épargne sur l’ensemble du circuit imprimé sauf aux endroits des soudures. Ceci facilite le soudage ultérieur notamment dans le cas de soudure par vague. X. Cahier des charges de réalisation d’une maquette. Un cahier des charges est un recueil de caractéristiques que doit présenter un matériel en cours de réalisation. Chaque maquette possède son propre cahier des charges énumérant ses contraintes spécifiques : - taille du circuit imprimé, - emplacement des connecteurs, - simple face, double faces ou multicouche, - utilisation de composants à piquer ou CMS, - etc. Il est tout de même possible d’énumérer quelques contraintes d’ordre général : • Les composants doivent être placés suivant une grille quadrillée en dixièmes de pouce (un trait tous les pas de 2,54 mm). L’unité utilisée par les logiciels de CAO est le millième d’inch : mil (un millième de pouce). Un pas est donc égal à 2,54 mm = 100 mil. • Les pistes de cuivres ne pouvant se croiser, il est parfois nécessaire lors de l’utilisation de circuit imprimé simple face, de recourir à des straps. Dans ce cas, le nombre de strap doit être minimum. Pistes Pistes Fig. X-a. Franchissement d'une piste à l'aide d'un composant et à l'aide d'un strap. Strap • Les composants doivent être le plus alignés possible. • Deux pistes doivent être séparées d’au moins ¼ de pas afin d’éviter les problèmes de développement photo du typon. • Afin d’éviter les problèmes de développement photo du typon, il faut respecter les règles suivantes : - Mis à part les pastilles des circuits intégrés, deux pastilles doivent être séparées d’au mois 200 mil. - La largeur des pistes doit être supérieure à 15 mil : on utilisera donc des pistes de 30 mil pour les connexions. - Dans la mesure du possible, uploads/Ingenierie_Lourd/ fabrication-maquette.pdf
Documents similaires
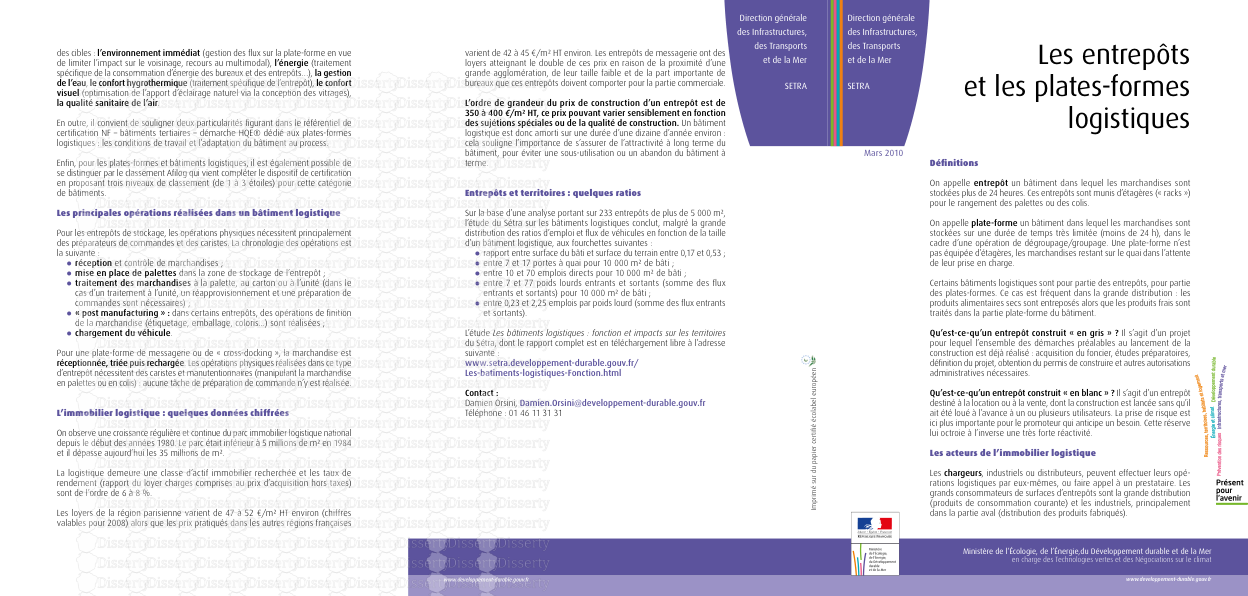
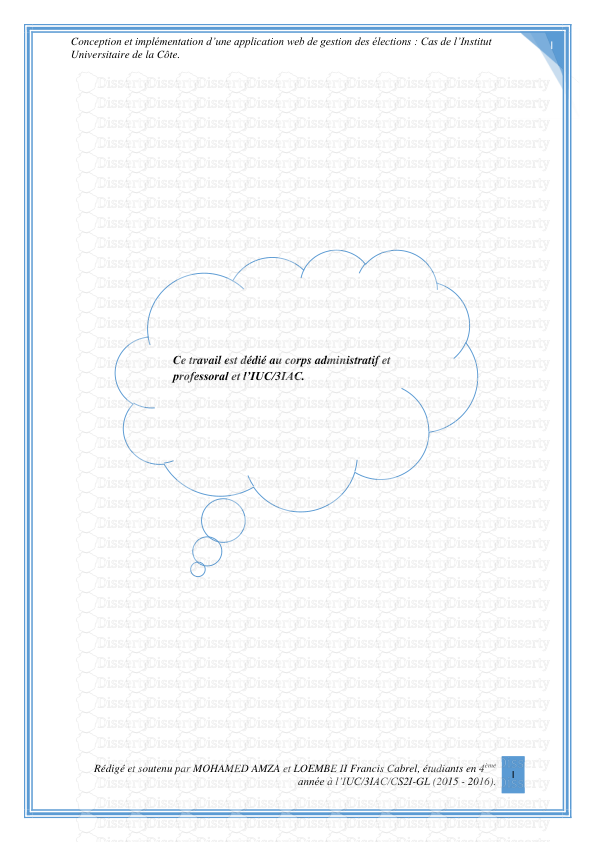
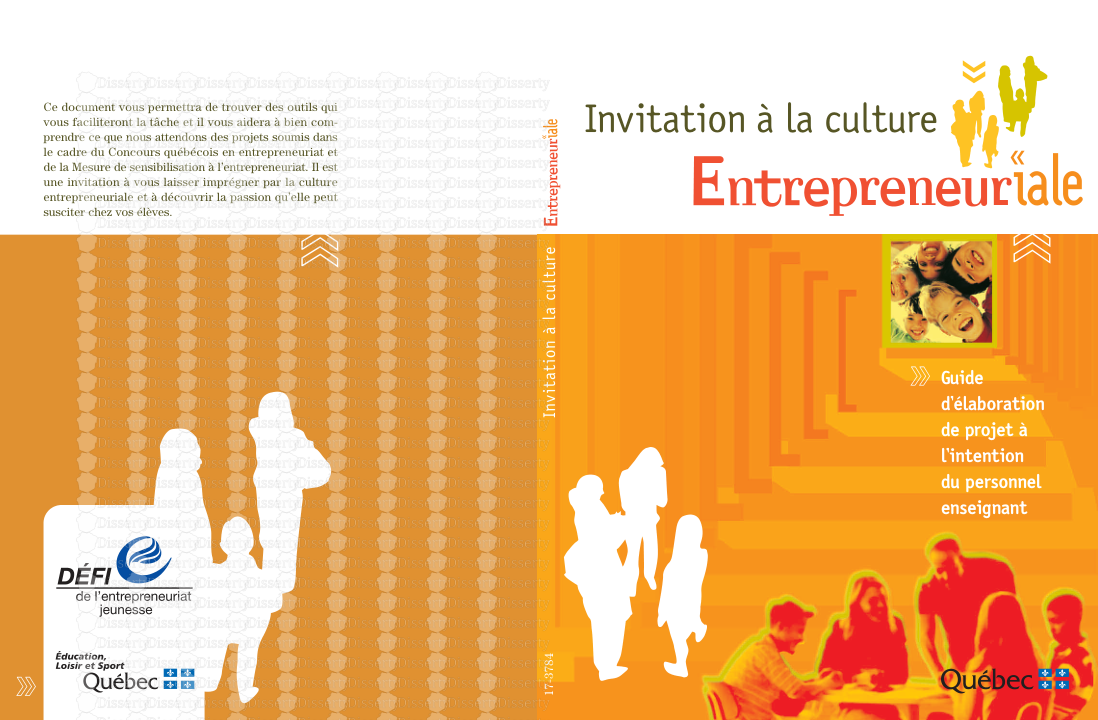
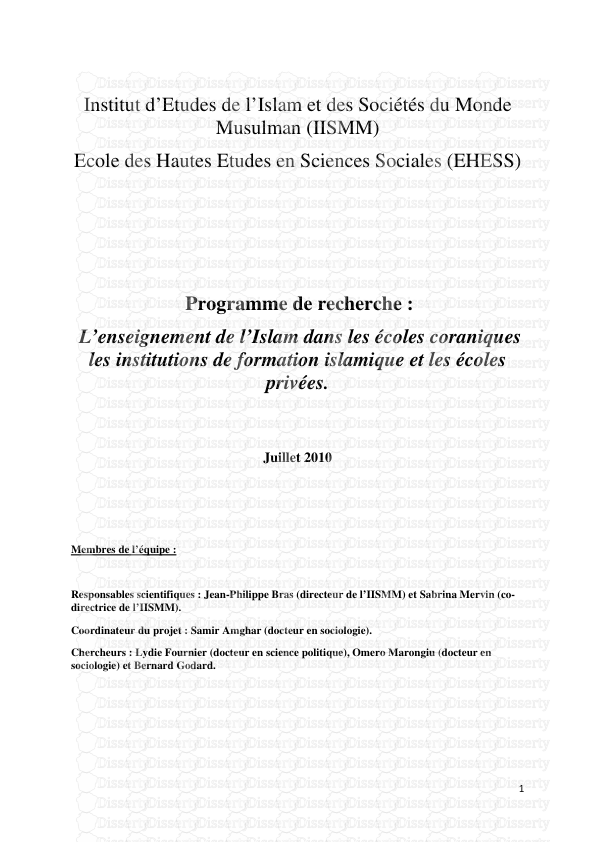
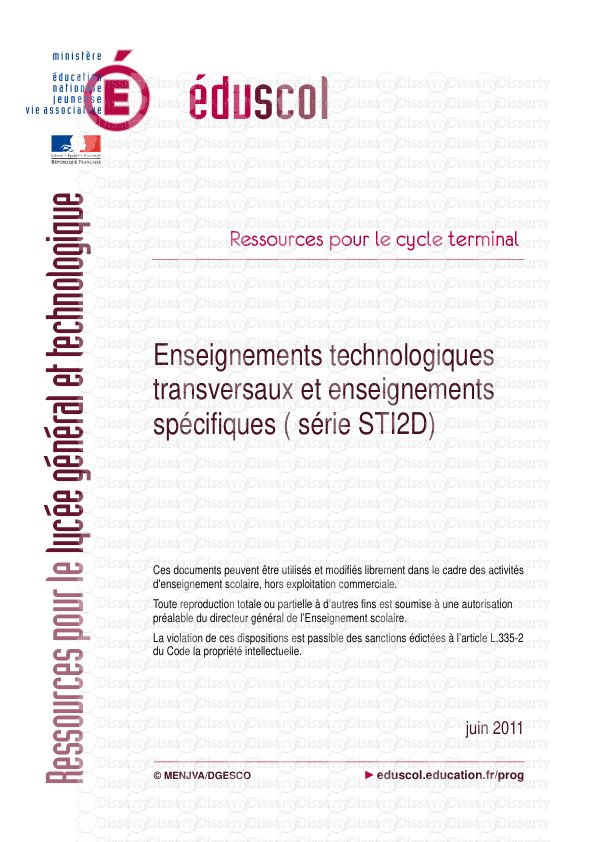
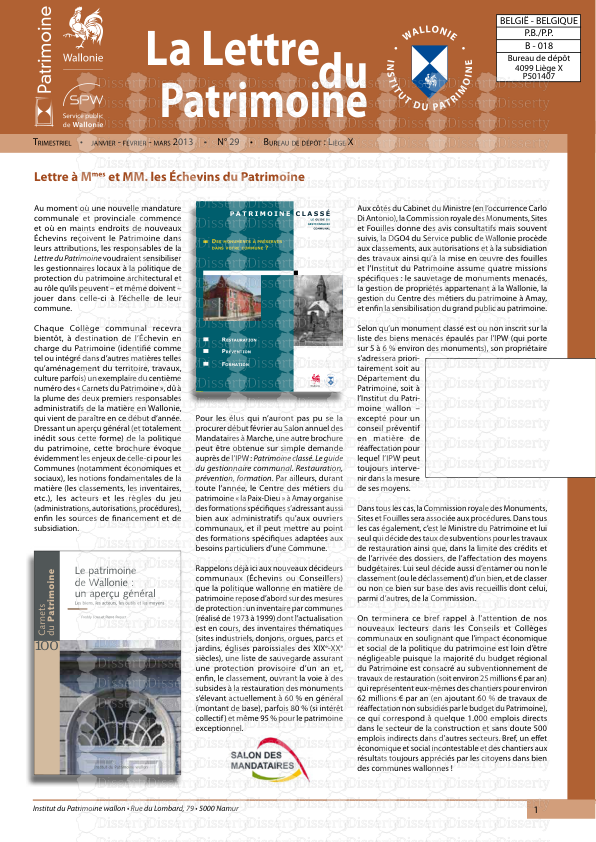
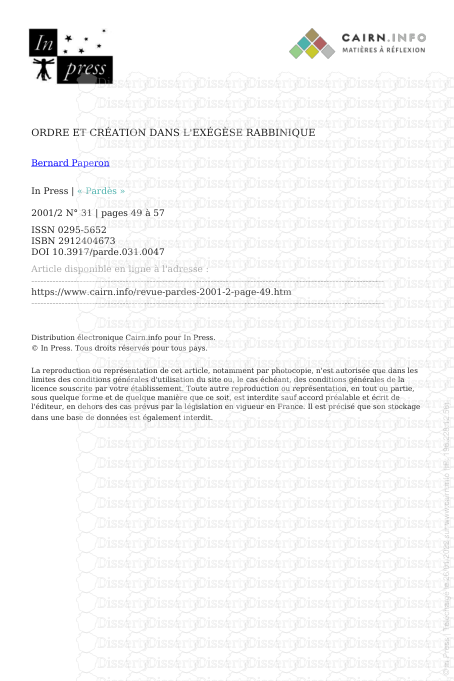
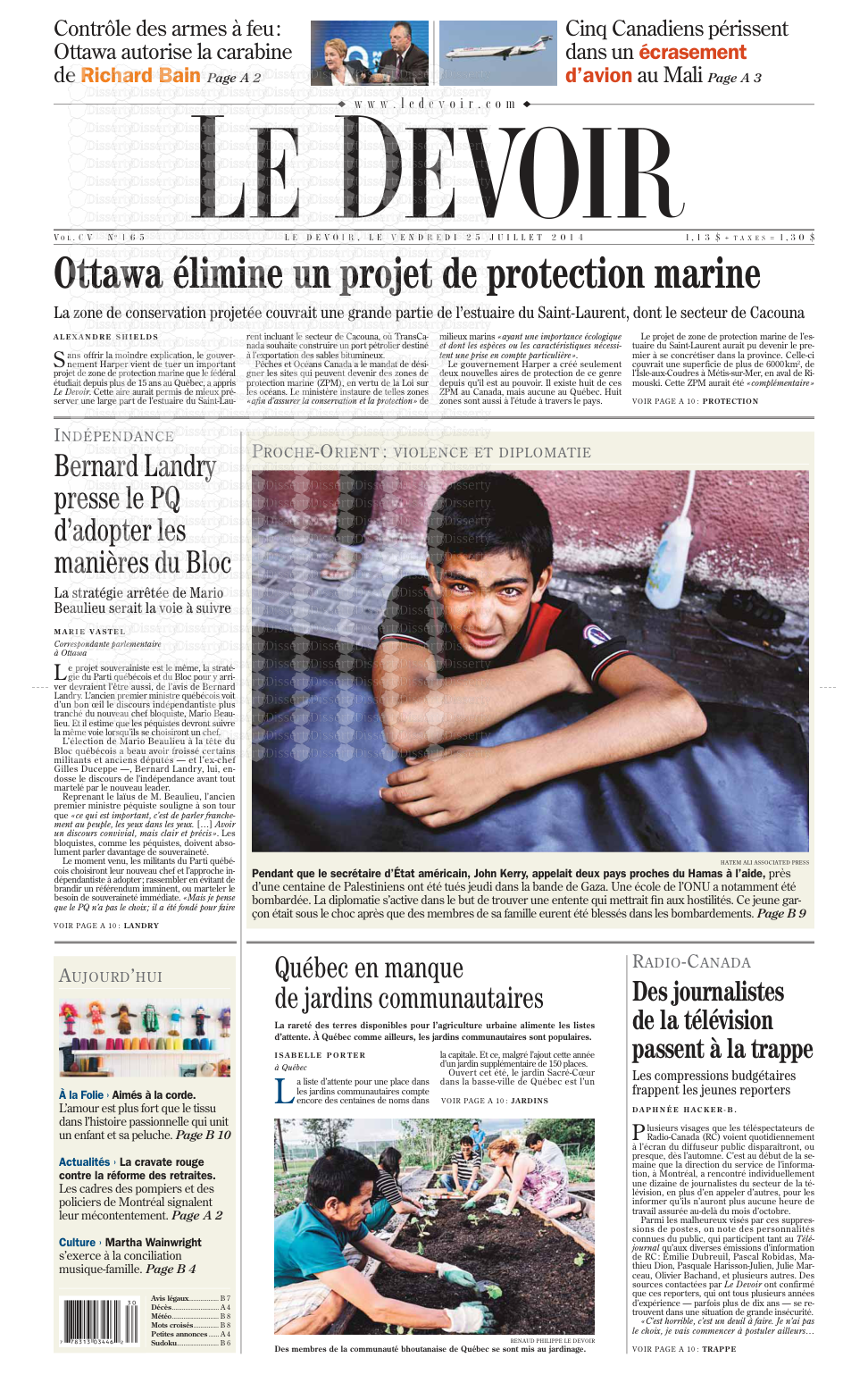
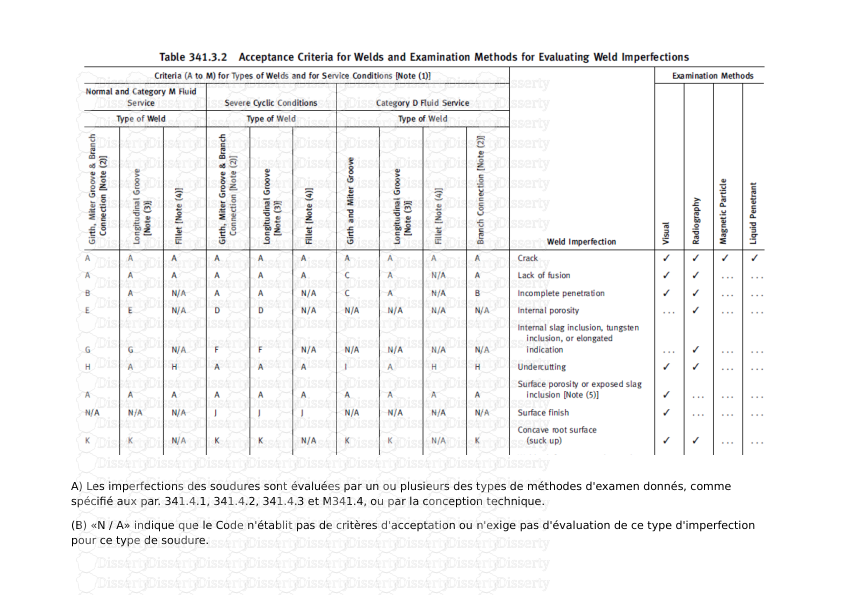
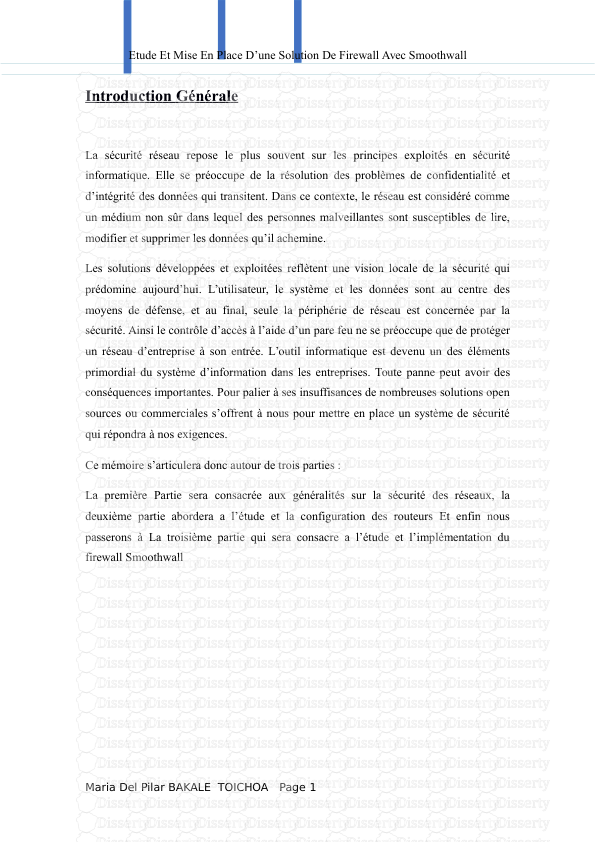
-
37
-
0
-
0
Licence et utilisation
Gratuit pour un usage personnel Attribution requise- Détails
- Publié le Sep 25, 2021
- Catégorie Heavy Engineering/...
- Langue French
- Taille du fichier 0.0981MB