Traitements et revêtements de surface (CVD/PVD) sur les parois des moules d'inj
Traitements et revêtements de surface (CVD/PVD) sur les parois des moules d'injection plastique. 1 : STIMAT : Support Technologique Interrégional en MATériaux avancés 2 : CRIF : Centre de Recherches des Industries Technologiques (Gosselies - BE) 3 : CRITT-MDTS : Centre Régional d’Innovation et de Transfert de Technologie, spécialisé dans les Matériaux, les Dépôts et les Traitements de Surface Juin 2005- p.1 de 4 1. Introduction La maîtrise des processus de fabrication est indispensable pour augmenter la productivité de nos entreprises. L’outillage représente une part importante du coût final de la pièce produite. Selon une étude menée par le CRIF, la conception d’un moule contribue à 15 % de son coût direct mais 50 % du coût final du produit moulé sont directement influencés par cette conception. Il est donc important de maîtriser la conception et les phénomènes qui en dépendent. Parmi ceux-ci, le moulage lui- même et le refroidissement sont actuellement bien maîtrisés grâce à la CAO et à l’ingénierie assistée par ordinateur (CAE). Il n’en va pas de même pour l’opération de démoulage, encore basée sur des connaissances souvent empiriques avec, en corollaire, l’absence de systématisme et de données objectives. Dans le cadre du projet Interreg III « STIMAT »1, le CRIF² et le CRITT- MDTS³ ont développé un projet visant à démontrer les avantages d'utilisation de traitements de surface de type PVD/CVD dans le cadre de la triple problématique classiquement rencontrée en injection : - faciliter le démoulage du produit moulé - accroître la durée de vie de l'outil - améliorer l’état de surface du produit élaboré tout en utilisant des technologies propres. Le but de cet article est de présenter les résultats obtenus au cours de 2 campagnes d’essais. 2. Objectifs L’objectif de ce projet vise à rencontrer une demande des moulistes et injecteurs confrontés à 5 problèmes : 1) les rebuts de production Ils sont dus la plupart du temps à des déformations ou des déchirures produites par un frottement excessif du polymère sur certaines parties de l’outillage. 2) l’usure consécutive à ces frottements ; 3) la corrosion le plus souvent engendrée par les produits de décomposition des polymères et des additifs ; Ces problèmes peuvent générer des arrêts de production et des réparations plus ou moins importants qui contribuent à diminuer la productivité de l’outil. Un autre phénomène doit également être pris en compte : 4) les batteries d’éjection trop importantes qui pénalisent le système de refroidissement et diminuent, par conséquent, la qualité de ce dernier. 5) Enfin, dans le monde extrêmement concurrentiel où évoluent les moulistes et les injecteurs, la productivité est un paramètre fondamental de la compétitivité. Cette productivité peut être atteinte en raccourcissant les temps de cycle, c. à d. en éjectant plus vite et par conséquent à une température plus élevée. Notons que les 4ème et 5ème problèmes sont liés : plus le système de refroidissement sera performant, plus vite on pourra éjecter sans devoir le faire à une température incompatible avec la rigidité du produit. Ces problèmes peuvent être résolus en améliorant les propriétés de surface des moules, c. à d. en choisissant des traitements de surface susceptibles de diminuer le frottement des matières injectées sur les parties « mâles » des moules lors de leur éjection. L’ensemble de cette problématique intéresse tous les moulistes et injecteurs. Toutefois, le projet a plus particulièrement été développé en pensant aux quelque 375 entreprises belges et françaises situées de part et d’autre de la frontière. 3. Dispositif et méthodologie La méthode consiste à injecter une pièce cylindrique de diamètre 60 mm, hauteur 30 mm et épaisseur 2 mm dans un moule dont le poinçon est sans dépouille et interchangeable. Lors de l’éjection, la pièce n’est en contact qu’avec le poinçon (moule à “coquilles”). La pièce est éjectée par une plaque dévêtisseuse mue par une batterie d’éjection munie d’un capteur de force. Pour chaque essai, la nature du revêtement du poinçon peut être modifiée tout en conservant les paramètres de moulage tels que température de la matière et température du moule, débits, pressions et temps. La constance des paramètres de moulage est systématiquement vérifiée par des capteurs au niveau du moule: - une température dans le poinçon (à mi-hauteur et à 2 mm de la surface) - une pression de moulage dans une coquille (face au capteur de t°) Outre la force de démoulage, le déplacement de la batterie et donc la vitesse d’éjection sont mesurées. Photo 1 : Moule “Cylindre” avec coquilles et plaque dévêtisseuse Fig. 1 : pièce d’essai (épaisseur 2 mm) 4 : POLYSTYROL 165H de BASF 5 : MACROLON 2800 de BAYER. 6 : SANTOPRENE 8281-55 de ADVANCED ELSTOMER SYSTEMS 7 : EVOPRENE 075 de ALPHAGARY 4. Les revêtements Les revêtements testés durant la 1ère campagne d’essais sont: - Ti Al N / TiN (2.3 µ) - Ti Al N (2.8 µ) - Cr N par pulvérisation (4.7 µ) - Cr N par sublimation ( -) - WC / C (4.4 µ) Dans un second temps, nous avons complété l’étude en testant : - CrN (0.293µ) - CrN (1.2µ) - CrN (1.7µ) - TiZrN (0.275µ) - TiZrCN (0.424µ) Dans les 2 cas, ces revêtements ont été comparés à des poinçons non revêtus de différentes rugosité. Les poinçons ont été réalisés en acier STAVAX ESR (Din 1.2083 – AISI 420 – AFNOR Z40 CNV 14) du fournisseur Uddeholm et ont subi un traitement thermique pour porter leur dureté à 54 HRC Les matériaux thermoplastiques testés ont été choisis pour leur difficulté de démoulage. Deux matériaux rigides ont été sélectionnés: - un polystyrène (PS) cristal 4 - un polycarbonate (PC) 5 Deux matériaux souples de type TPE (thermoplastique élastomère) ont été également sélectionnés: - un thermoplastique à vulcanisation réversible (TPV) à base de PP-EPDM 6 - un styrène-éthylène-butylène- styrène (SEBS) 7 5. La mesure des forces de démoulage La figure 2 ci-contre montre les 4 paramètres enregistrés lors de chaque éjection. 6. Les résultats Les deux tableaux, page suivante, synthétisent les 2 campagnes réalisées. Chaque tableau de synthèse représente le résultat de plusieurs milliers de mesures. Il s’agit de valeurs moyennes et les écarts (≤ 10 %) ne sont pas indiqués afin de conserver la lisibilité. Les conditions d’essais pour chaque revêtement et chaque matière ont toujours été aussi comparables que possible mais réalisées dans des situations (e.g. : t°, P, humidité et taux de poussières ambiants variables), correspondant à celles rencontrées généralement dans l’industrie. La première campagne (tableau 1) nous a permis de constater que les revêtements en TiAlN offrent un avantage évident pour l’éjection de produits en polycarbonate. Les autres couples « revêtements- matériaux » ne semblent pas réagir de la même manière. Sur cette base, une seconde campagne d’essais a été menée. Elle avait pour objectif de tester deux matières (le PC Macrolon qui avait fourni des résultats prometteurs et du PUR Desmopan 385C) avec des nouveaux traitements de surface (Ti ZrN et Ti Zr CN) et de les comparer avec des revêtements connus (CrN) et des non revêtus de rugosités différentes. Les résultats obtenus figurent dans le tableau 2. Ils sont tout aussi difficiles à interpréter que ceux résultant de la première campagne. A titre d’exemple, si le CrN semble jouer globalement un rôle négatif, il est difficile d’imaginer qu’une diminution de rugosité (Ra = 0.293µ) puisse jouer un tel rôle sur la force nécessaire à éjecter le PUR (6 fois plus grande qu’un CrN ayant un Ra = 1.7µ). Fig. 2 : Macrolon 2800 / TiAlN-TiN Fig. 3 : force de démoulage en fonction du revêtement PC Makrolon 2800 700 750 800 850 900 950 1000 TiALN-TiN TiAlN CrN Pulv CrN Evap WC/C Non revêtu Type de revêtement Force de démoulage (N 8 : Amélioration des outillages d’injection par optimisation de nouveaux revêtements (B. LE RAZER - Pôle européen de plasturgie – Visions (supplément technique n°6) Mai 2004 7. Les conclusions Il semble donc impossible de tirer des lois de comportement général des couples « matériaux injectés – revêtements de surface ». Tout au plus peut-on constater qu’un revêtement de surface déterminé peut favoriser – par rapport à un poinçon non revêtu - l’éjection d’un matériau injecté déterminé mais que ce même revêtement peut freiner l’éjection d’un autre matériau. Cependant, la littérature 8 nous a récemment fourni quelques indications. Avec toutes les précautions d’usage car les conditions expérimentales (type de moule, machine à injecter, environnement, dépouille, …) sont différentes, B. Le Razer du Pôle Européen de Plasturgie conclut : « Il a été démontré qu’il n’existe pas de revêtement universel protecteur permettant de remédier aux problèmes de frottement et de collage des polymères testés, contrairement à ce que pensaient initialement les industriels. En effet, les résultats sont intrinsèques à la nature du polymère injecté et à la nature de la surface de l’outillage.». Il ajoute : une classification des revêtements a été établie pour chaque polymère testé, ce qui a permis de sélectionner les meilleurs traitements pour la validation industrielle : - Choix pour PP et PA + 30% GF : TiAlN et SiOx - Choix uploads/Industriel/article-mum-at.pdf
Documents similaires
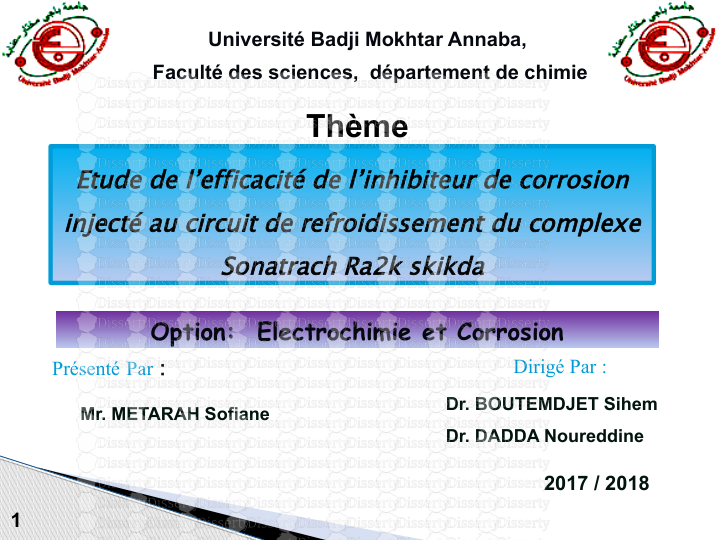

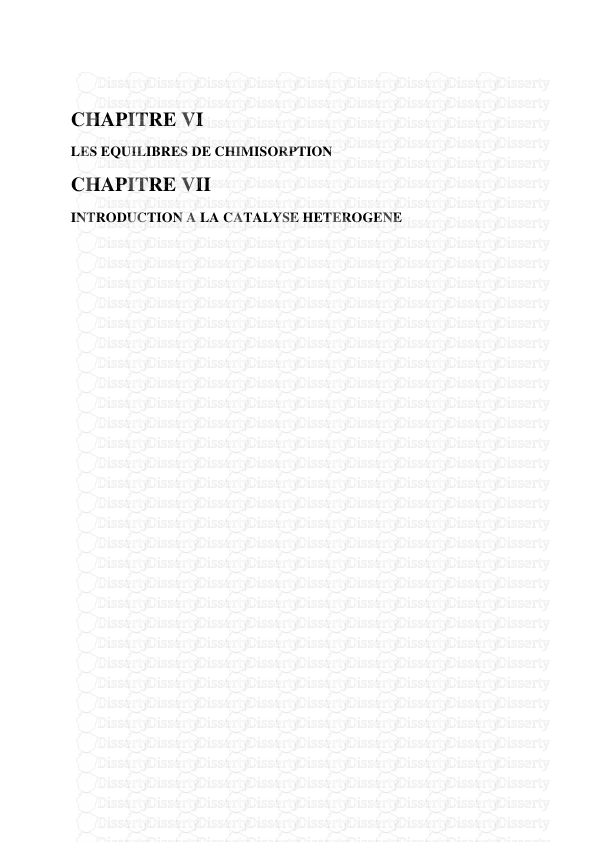
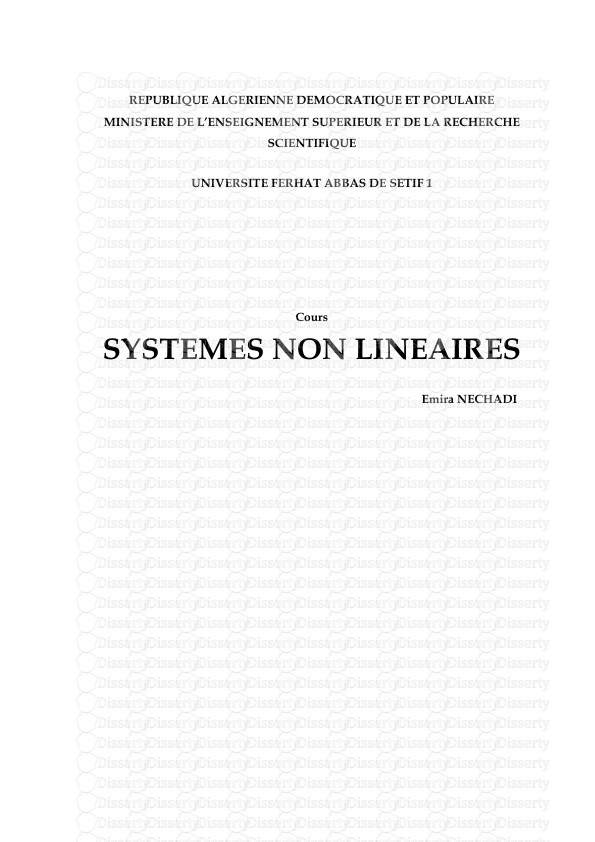
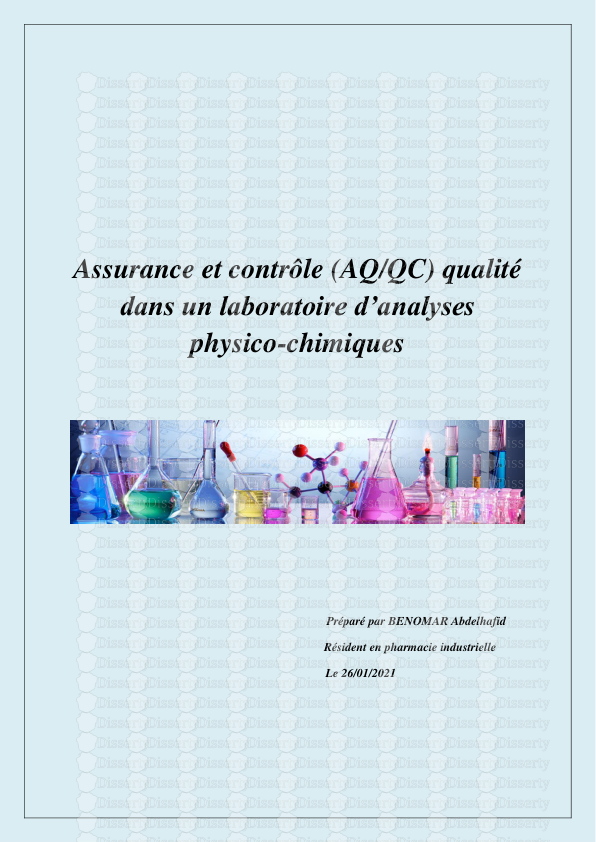

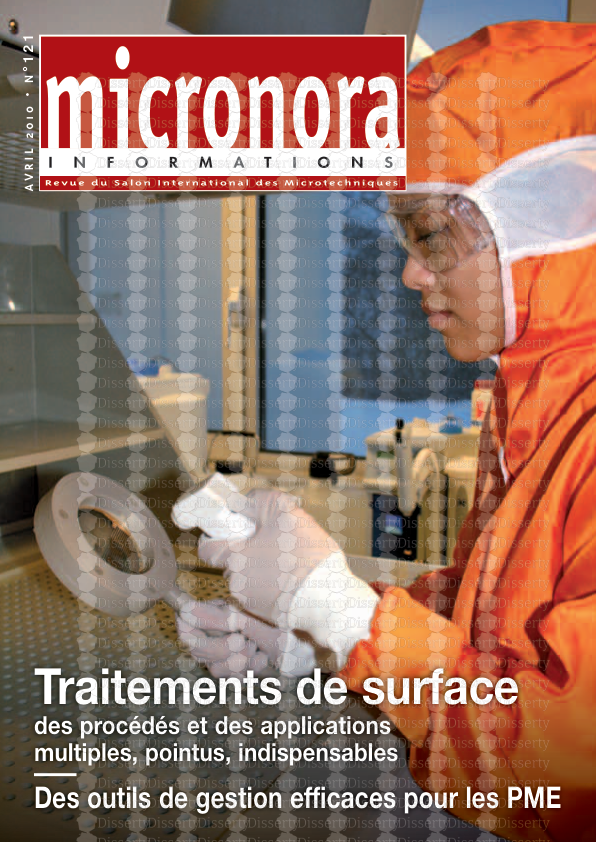
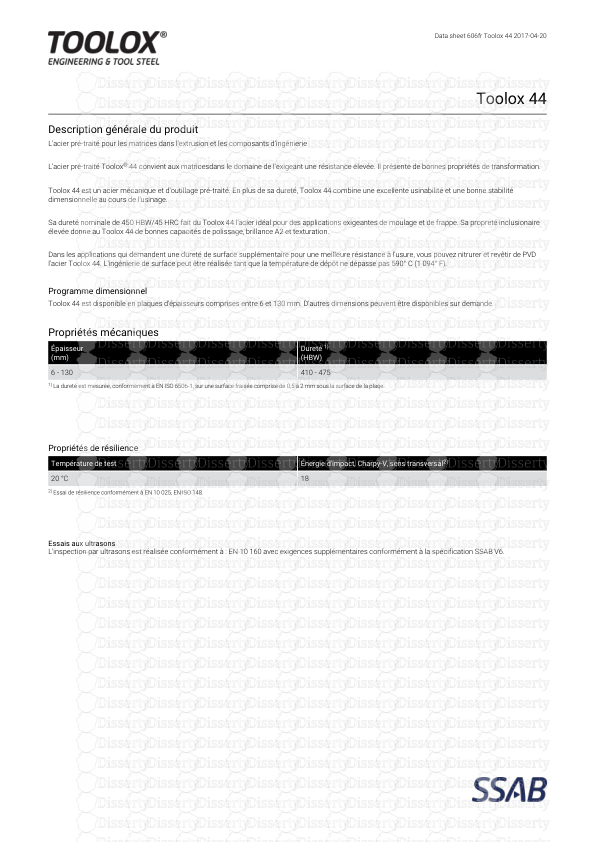
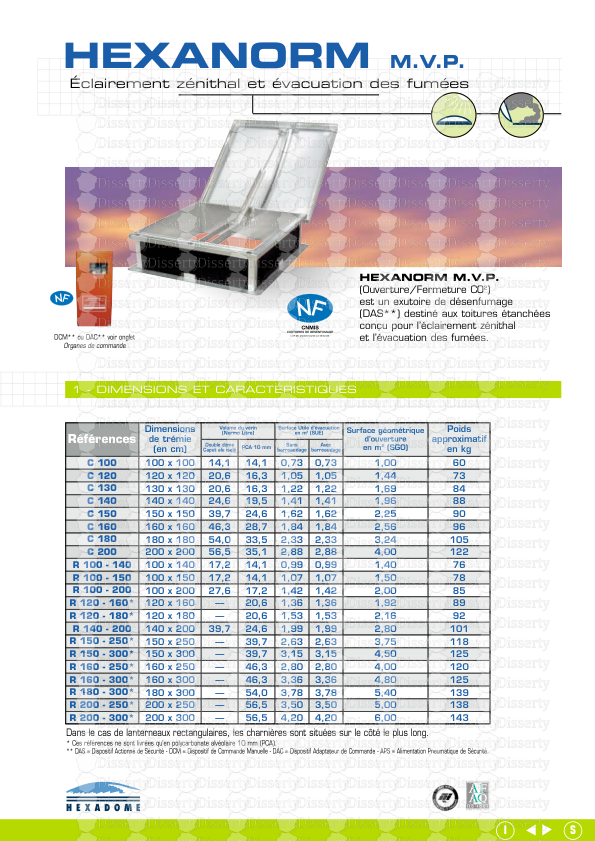
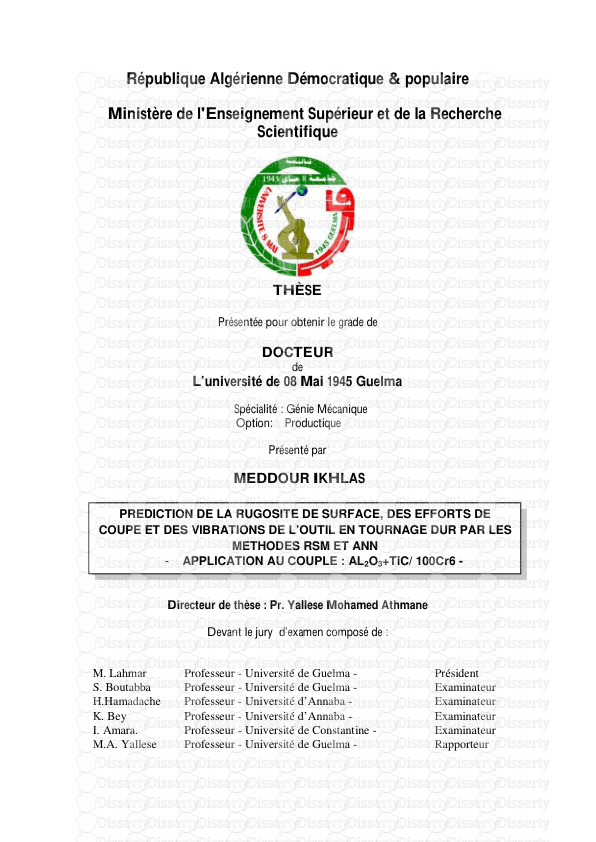
-
37
-
0
-
0
Licence et utilisation
Gratuit pour un usage personnel Attribution requise- Détails
- Publié le Mar 04, 2021
- Catégorie Industry / Industr...
- Langue French
- Taille du fichier 0.2174MB